
كل ما يتعلق بمخطط إيشيكاوا
Public Space
4 minutes
Understanding the Ishikawa Diagram for Effective Project Management with Enlaps' Tikee Camera
Want to know about the Ishikawa Diagram definition? An Ishikawa Diagram, also known as a "fishbone diagram," is one of the essential project management used for issue management tools. This tool helps identify the root causes of faults, deviations, or failures in a process. By breaking down underlying factors, it aids in understanding what impacts subsequent levels of a project. Curious about which tools are used for project management? Let’s dive in.
The issues in any company can be categorized into six distinct kinds of significant reasons that impact the whole process: machines, materials, manpower, mother nature, measurements, and methods. These are commonly referred to as the 6 M's of the Ishikawa Diagram.
It is worth noticing that all of these reasons begin with the letter "M.”. As a result, these reasons are often known as the 6 M's of the Ishikawa Diagram.

The 6 Ms of the Ishikawa Diagram
Read on to find what comprises the Ishikawa diagram
Machine
Machines and equipment breakdowns are the sources of a lot of root issues. This may be the result of poor or non-existent upkeep.
The usage of materials in the process is the source of this problem. This may be due to out-of-spec material or an inaccurate volume.
Manpower or team
It has to do with workers' attitudes throughout the performance of tasks. Their hurry, irresponsibility, lack of qualification, or even lack of motivation may contribute to this problem.
Mother Nature
These are issues with the organization's internal and external environments.
For example, while discussing external issues, you might bring up pollution and weather instability. Internally, there may be a shortage of room, an improper arrangement, or noise, among other things.
Measurements
This "M" in the Ishikawa diagram or fishbone diagram definition stands for metrics used to measure, manage, and monitor operations.
You may be measuring your process incorrectly. This causes rework and slows down your workflow.
Methods
The processes and techniques used by the organization during activities are referred to as procedures and methods.
Software and planning tools may be used to define the approach. It depicts how you plan the progression of your activities and how you keep track of what's going on.
The Concept
Ishikawa was an engineer who worked for the Japanese Union of Scientists and Engineers, and the University of Tokyo. He eventually expanded on an annotation concept he had - demonstrating branching causation between issue antecedents and a recognized consequence. This wasn't the first effort at anything similar, but it was the most well-organized.
He started with simple branches from major causal factor categories like types of equipment and machinery, then branching out to anything that a person may have been involved with (or if there were root issues that could have been avoided by personnel), and finally branching out to the facility itself (i.e., were there any deficiencies in the facility that could have led to an identified problem).
Variation is the kryptonite of quality and efficiency in almost every sector or company. After an order is placed, a consistent and uniform procedure should be followed through delivery. Variation in that procedure almost always translates to variation in the end output.
Fishbone diagrams are a useful tool for determining possible variables in a process to prevent faults or failures or for determining what is causing a defect or failure that has already occurred.
Making an Ishikawa Diagram: A step-by-step guide
Things you will need to make an Ishikawa (or fishbone) diagram:
A whiteboard, a flip chart, and some marking pens
The whole group should agree upon an issue statement.
In the flipchart or whiteboard centre-right corner, write the issue statement, box it, and draw a horizontal arrow to it.
Identify and make a list of the main or root causes of the issue. For example, starting with these general headings: techniques, machines (equipment), people (manpower), materials, measurement, and environment may be a good place to start.
The types of issues should be written as branches from the main arrow.
Make a list of potential reasons. "Why does this happen?" you may wonder. The facilitator notes each concept as a branch from the relevant category as it is presented. If a cause is related to several categories, it may be written in multiple locations.
Rephrase the inquiry, "Why does this happen?" Frame some sub–causes that separate the main causes. Continue to ponder the question "Why?" to uncover deeper layers of reasons. Layers of branches represent Cause-and-effect connections.
When the team is at a loss for ideas, pay special attention to the diagram or chart regions where ideas are few.
The Fishbone Diagram is a very effective instrument of quality, regardless of how you use it. When these diagrams are used consistently and often, they will assist you to identify underlying causes of difficulties (rather than simply causative variables) and develop CAPAs to address those issues.
In reality, “standardization” and “quality control” are “two wheels of the same cart,” according to Ishikawa. This is also true in the quest for product quality. If you don't have strict rules or proper training for implementing quality procedures, especially during improvement investigations, you're losing control of the quality.
For more information on how Enlaps' Tikee cameras can enhance your project management processes, visit Enlaps.
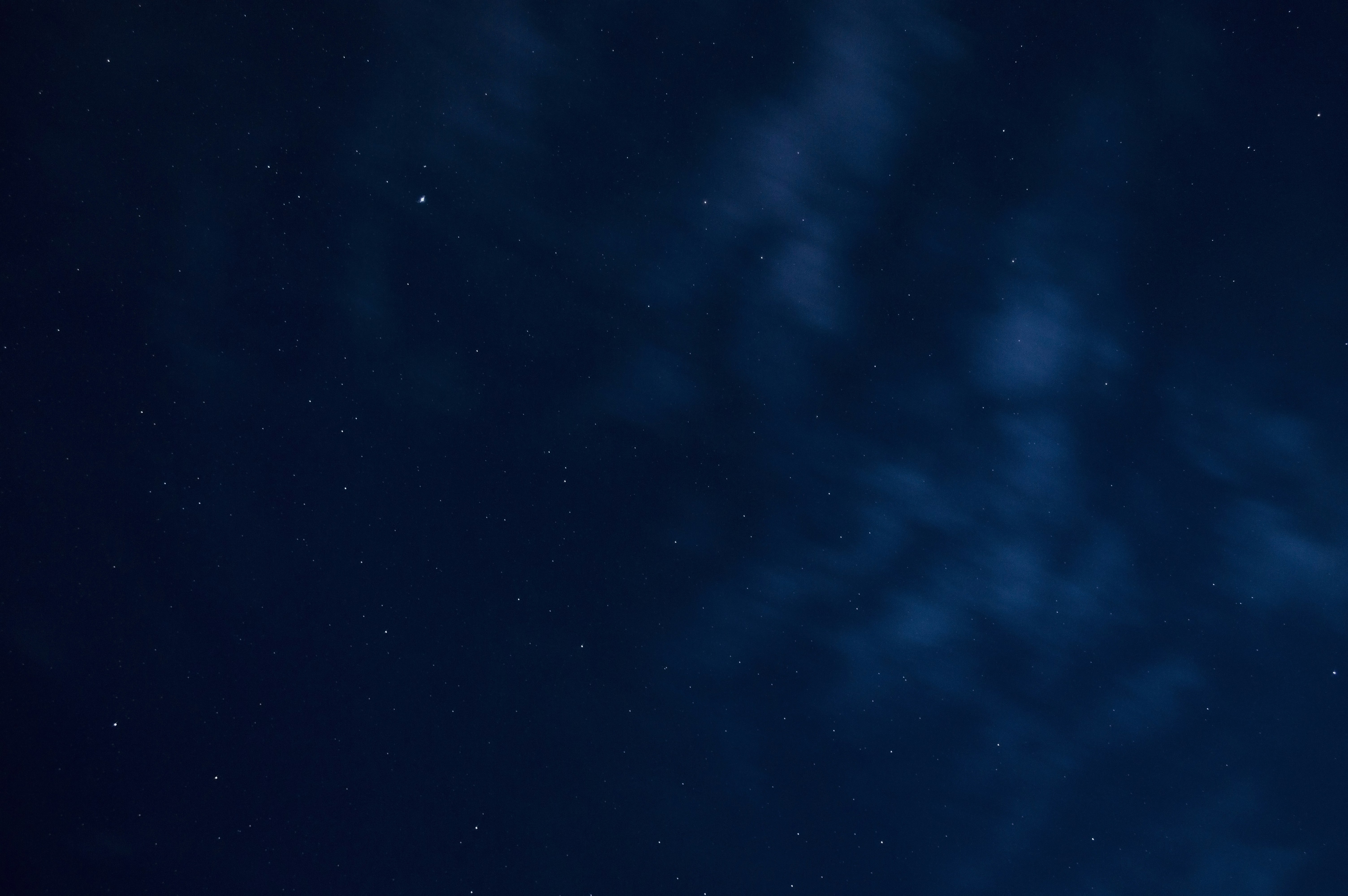
النشرة الإخبارية
سجّل للحصول على نشرتنا الإخبارية
احصل على آخر الأخبار، العروض الحصرية، دراسات الاستخدام، والنصائح الخبرة بالتسجيل الآن!
في حاجة إلى عرض توضيحي مخصص
لفهم حل تايم لابس بشكل أفضل ولمعرفة المزيد قبل البدء، نقدم لكم تحديد موعد فردي، عبر مؤتمر فيديو.