
All About Ishikahwa Diagram
Public Space
4 minutes
Understanding the Ishikawa Diagram for Effective Project Management with Enlaps' Tikee Camera
Interested in the definition of the Ishikawa Diagram? The Ishikawa Diagram, also known as a "fishbone diagram," is a crucial tool for project management, employed for resolving issues. It assists in pinpointing the fundamental causes of defects, variations, or failures within a process. By dissecting the contributing factors, it facilitates comprehension of how they influence subsequent project stages. Wondering about the tools used in project management? Let's delve into that.
Within any business, issues can be sorted into six primary categories of root causes that affect the entire process: machines, materials, manpower, mother nature, measurements, and methods. These are frequently called the 6 M's of the Ishikawa Diagram.
It is significant to note that each of these categories begins with the letter "M,” hence, they are often termed the 6 M's of the Ishikawa Diagram.

The 6 Ms of the Ishikawa Diagram
Continue reading to discover what constitutes the Ishikawa diagram
Machine
Machine and equipment malfunctions are often at the heart of many issues. This might stem from inadequate or nonexistent maintenance.
The use of materials in the process often causes problems. This could be due to material that does not meet specifications or incorrect quantities.
Manpower or Team
This relates to the behavior of workers during task execution. Their rush, negligence, insufficient qualification, or even a lack of motivation might be contributors to these issues.
Mother Nature
These issues pertain to the internal and external environments of the organization.
Externally, you could mention pollution and unpredictable weather. Internally, constraints like limited space, poor layout, or noise could be factors.
Measurements
This "M" in the Ishikawa diagram refers to the metrics for measuring, controlling, and monitoring operations.
Mismeasuring your process can result in redoing work and decelerating your workflow.
Methods
The organization's operational processes and techniques are known as procedures and methods.
Software and planning tools might define the methodology. It represents how you plan the course of your activities and monitor progress.
The Concept
Ishikawa was an engineer affiliated with the Japanese Union of Scientists and Engineers and the University of Tokyo. He further developed a concept he had regarding the visual representation of causation between precursors of a problem and an identified result. While not the first attempt at such an approach, it was notably well-structured.
He began with primary branches from major causal factors like types of equipment, then expanding to involvement of individuals (or potential personnel-related issues), and ultimately to the facility itself (i.e., identifying if there were any shortcomings at the facility that could lead to problems).
Variability is detrimental to quality and efficiency in virtually all industries. After an order is placed, the process should be consistent and standardized all the way to delivery. Variability in the process often means variability in the final product.
Fishbone diagrams prove valuable in pinpointing potential factors in a process that could prevent issues or identify the cause of an existing defect or failure.
Constructing an Ishikawa Diagram: A Step-by-Step Guide
Items needed for creating an Ishikawa (or fishbone) diagram:
A whiteboard, flip chart, and markers
Consensus on a problem statement by the entire team.
Write the problem statement on the flip chart or whiteboard, box it, and draw a horizontal arrow leading to it.
Identify and enumerate the primary or fundamental causes. For example, begin with general categories such as procedures, machines (equipment), people (manpower), materials, measurements, and environment.
Branches from the main arrow should represent the types of issues.
List potential causes. You may ask, "Why does this occur?" As each idea is suggested, it's recorded as a branch from the corresponding category. If a cause relates to several categories, record it in each relevant spot.
Repeat the question, "Why does this occur?" Develop sub-causes that expand on the main ones. Continue probing with "Why?" to discover deeper layers of reasons. These layers of branches show Cause-and-effect links.
When ideas run dry, focus on areas of the diagram with fewer suggestions.
The Fishbone Diagram is an incredibly effective quality tool. When applied consistently, it aids in spotting the underlying causes of issues (rather than just symptoms) and in creating corrective and preventive actions (CAPAs) to solve those issues.
Indeed, "standardization" and "quality control" are akin to "two sides of the same coin," as noted by Ishikawa. This holds true in the pursuit of product quality. Without stringent guidelines or thorough training in applying quality processes, particularly during remediation investigations, you risk losing control over quality.
For further details on how Enlaps' Tikee cameras can enhance your project management practices, visit Enlaps.
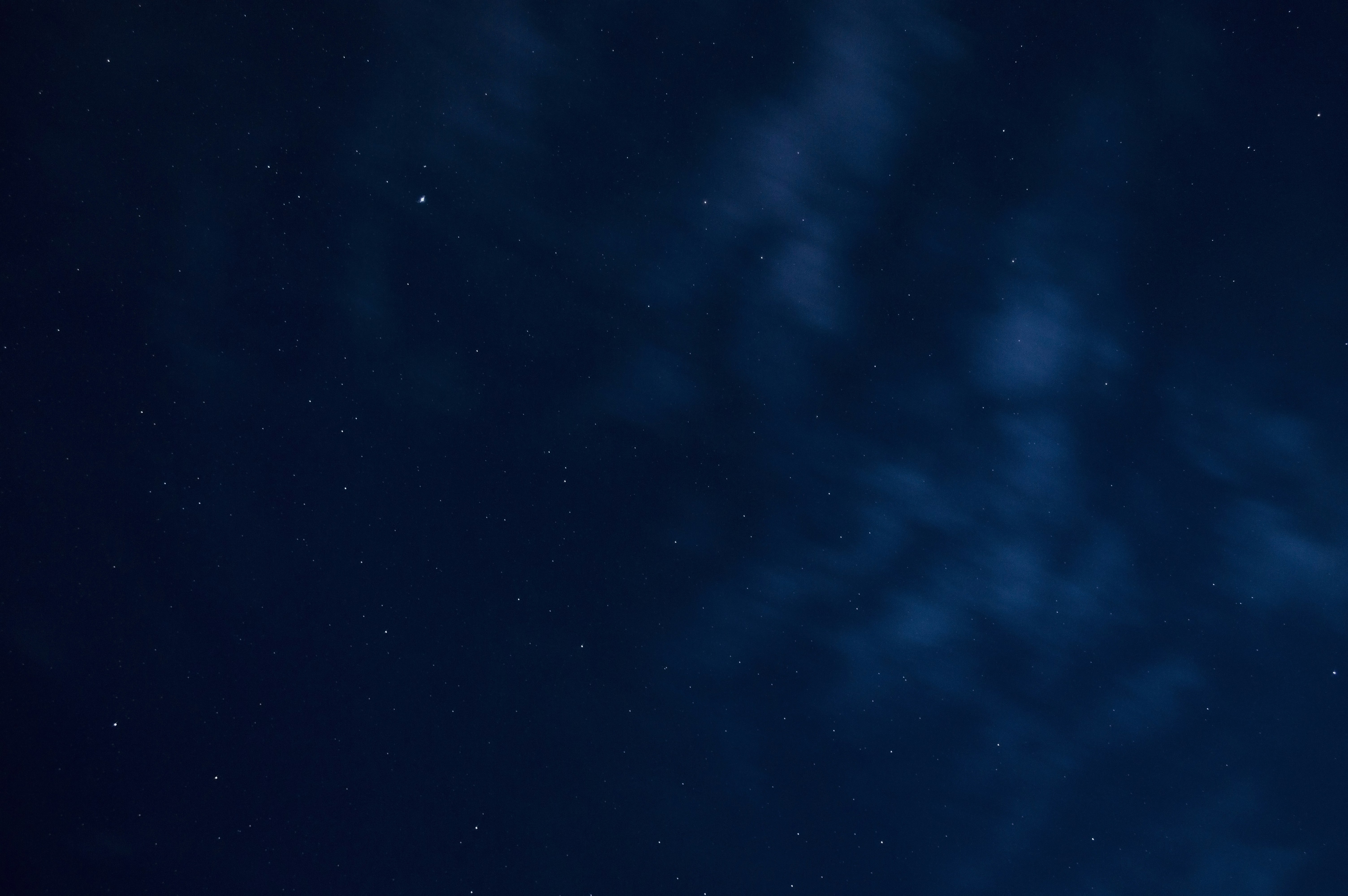
Newsletter
Subscribe for our newsletter
Get the latest news, exclusive offers, use cases, and expert advice by signing up now!
Need a personalized demonstration
To better understand the Tikee solution and to learn more before getting started, we offer you the opportunity to schedule a one-on-one appointment, via video conference.